導讀:卷對卷印刷生產流程憑借其節約紙張的優勢而得到了特別的重視。筆者將在煙包卷對卷燙印質量優化控制過程中遇到的問題和解決方法與各位同行分享。
工藝流程優化設計
卷對卷燙印的優勢是可以采用無縫拼版的方式來節約紙張,因此卷對卷燙印后必須配套圓壓圓模切才能更好地發揮出該優勢。
然而,由于卷對卷生產涉及的設備較多,需要對每臺設備的特殊要求都要全面關注。特別是凹印張力控制尤其重要,需要在打樣試機過程中確定每臺設備的張力控制數值,且在后續正常生產時該設定值不能做過大調整,否則帶來的套印、模切不準問題會相當嚴重。
在印前排版時,還需全面考慮不同設備的套準、糾偏系統對套印標記、檢測線的位置和尺寸的特殊要求,能共用的套印標記最好整個工藝流程共用一個,實在不能共用的套印標記也要盡量使用同一種顏色,以保證套印精度。
設備優化改造
由于不同的煙包產品具備不同的特殊性能,因此對燙金設備的要求也不盡相同。為此,筆者公司對現有設備進行了以下幾個方面的優化改造,以使其更好地適應煙包產品的燙印生產。
1.導紙滾筒表面特殊處理
在生產以轉移金卡紙為承印材料的硬包小盒時出現套燙印無規律跑動現象,加大設備張力、調整套準系統、調整凹印張力均無法徹底解決,而使用普通白卡紙印刷的其他煙包產品均正常。
原因是紙張在走紙過程中產生打滑,進而出現套燙印無規律跑動現象。于是對導紙滾筒表面進行了特殊處理,使用摩擦力較大的材料進行包裹,增加導紙滾筒表面的摩擦力,減少紙張在走紙過程中產生打滑的幾率,套燙印無規律跑動現象由此得以解決。
2.氣脹軸安裝位置優化改造
在生產軟包小盒時出現收卷后紙張起皺現象,造成的廢品比例較高。
經分析,該煙包產品使用的是定量為97g/m2的單面銅版紙,紙張較薄,每卷紙張長度約為8400米,當燙印至紙卷卷芯部分時,因設備收卷裝置的機械間隙過大而造成紙張擺動較大,從而形成紙張起皺現象。
對設備收卷裝置氣脹軸的安裝位置進行優化改造,即在機器墻板上加裝新的旋轉支撐架,將軸承套位固定在新支撐架的三個軸承上,消除機械間隙,徹底解決收卷后紙張起皺現象。
3.加裝粘膠滾筒
在生產軟包小盒時出現燙印后產品表面存在少量金粉問題,與電化鋁供應商多次溝通調整電化鋁參數后,仍未能徹底解決。
經過分析后,在設備上增加一組裝置,使用對產品質量無影響的粘膠滾筒對燙印后產品表面的少量金粉進行吸附。使用該裝置后,產品質量得到了提升。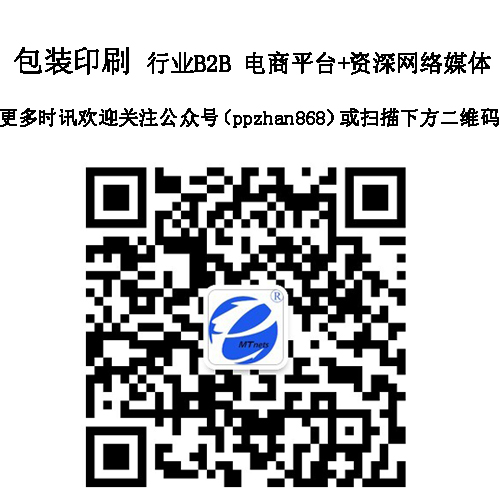
工藝流程優化設計
卷對卷燙印的優勢是可以采用無縫拼版的方式來節約紙張,因此卷對卷燙印后必須配套圓壓圓模切才能更好地發揮出該優勢。
然而,由于卷對卷生產涉及的設備較多,需要對每臺設備的特殊要求都要全面關注。特別是凹印張力控制尤其重要,需要在打樣試機過程中確定每臺設備的張力控制數值,且在后續正常生產時該設定值不能做過大調整,否則帶來的套印、模切不準問題會相當嚴重。
在印前排版時,還需全面考慮不同設備的套準、糾偏系統對套印標記、檢測線的位置和尺寸的特殊要求,能共用的套印標記最好整個工藝流程共用一個,實在不能共用的套印標記也要盡量使用同一種顏色,以保證套印精度。
設備優化改造
由于不同的煙包產品具備不同的特殊性能,因此對燙金設備的要求也不盡相同。為此,筆者公司對現有設備進行了以下幾個方面的優化改造,以使其更好地適應煙包產品的燙印生產。
1.導紙滾筒表面特殊處理
在生產以轉移金卡紙為承印材料的硬包小盒時出現套燙印無規律跑動現象,加大設備張力、調整套準系統、調整凹印張力均無法徹底解決,而使用普通白卡紙印刷的其他煙包產品均正常。
原因是紙張在走紙過程中產生打滑,進而出現套燙印無規律跑動現象。于是對導紙滾筒表面進行了特殊處理,使用摩擦力較大的材料進行包裹,增加導紙滾筒表面的摩擦力,減少紙張在走紙過程中產生打滑的幾率,套燙印無規律跑動現象由此得以解決。
2.氣脹軸安裝位置優化改造
在生產軟包小盒時出現收卷后紙張起皺現象,造成的廢品比例較高。
經分析,該煙包產品使用的是定量為97g/m2的單面銅版紙,紙張較薄,每卷紙張長度約為8400米,當燙印至紙卷卷芯部分時,因設備收卷裝置的機械間隙過大而造成紙張擺動較大,從而形成紙張起皺現象。
對設備收卷裝置氣脹軸的安裝位置進行優化改造,即在機器墻板上加裝新的旋轉支撐架,將軸承套位固定在新支撐架的三個軸承上,消除機械間隙,徹底解決收卷后紙張起皺現象。
3.加裝粘膠滾筒
在生產軟包小盒時出現燙印后產品表面存在少量金粉問題,與電化鋁供應商多次溝通調整電化鋁參數后,仍未能徹底解決。
經過分析后,在設備上增加一組裝置,使用對產品質量無影響的粘膠滾筒對燙印后產品表面的少量金粉進行吸附。使用該裝置后,產品質量得到了提升。
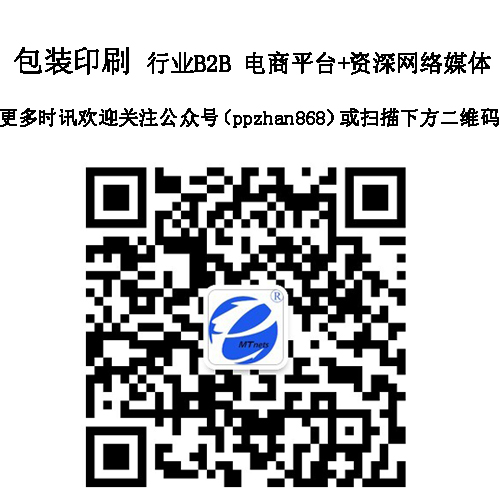